How robots are transforming manufacturing industries
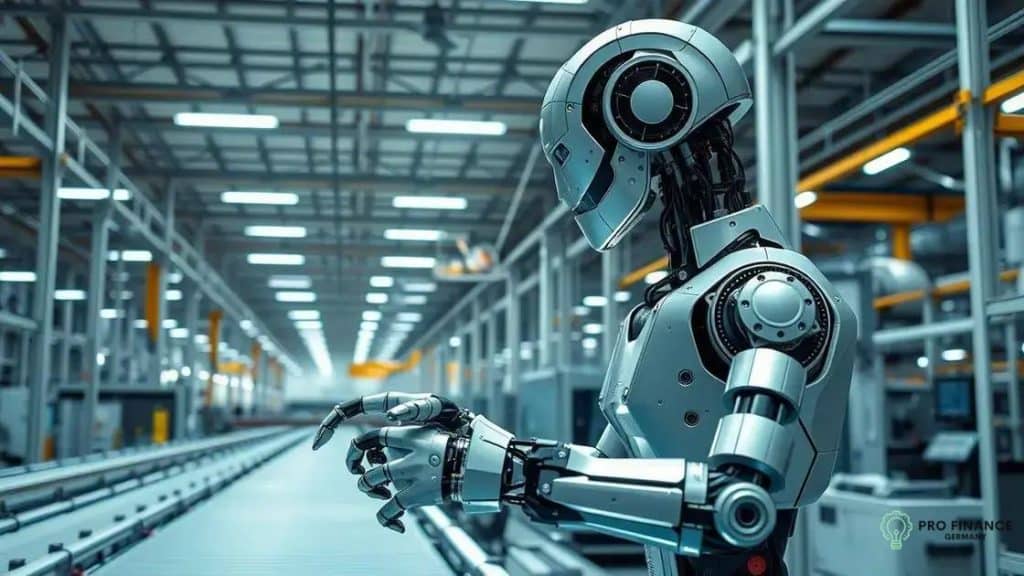
Robots are transforming manufacturing industries by enhancing efficiency, reducing costs, and improving product quality through automation and advanced technologies.
How robots are transforming manufacturing industries is a question many are asking as we advance into an age of automation. Have you ever wondered how these machines are reshaping production processes and improving efficiency? In this article, we’ll explore the transformative impact of robotics on modern manufacturing.
The rise of robotics in manufacturing
The rise of robotics in manufacturing has changed the way factories operate. Robotics has made processes faster, safer, and more efficient. With the advent of advanced technology, manufacturers can now implement robots to perform tasks traditionally done by humans.
Types of Robots Used in Manufacturing
There are several types of robots utilized in the manufacturing sector:
- Articulated Robots: These are the most common, resembling a human arm.
- SCARA Robots: These are perfect for assembly operations due to their high speed.
- Delta Robots: Known for their quick movement, ideal for packaging tasks.
Each type serves specific functions and brings unique advantages to manufacturing processes. This diversity allows companies to optimize their production line according to their needs.
Impact on Workforce
While some fear that robots may take jobs, they also create new employment opportunities. Robotics requires skilled workers to operate, maintain, and program these machines. This shift means that education and training in technology are becoming increasingly important.
The integration of robots into manufacturing not only improves productivity but also enhances product quality. With machines performing repetitive tasks, the rate of errors decreases, leading to consistent results. As industries evolve, robotics continues to play a crucial role in driving innovation.
Furthermore, the use of robots contributes to worker safety. Dangerous tasks can be assigned to machines, reducing the risk of workplace injuries. As a result, employees can focus on complex and creative problem-solving tasks that require human insight.
The rise of robotics is transforming the landscape of manufacturing industries, signaling a new era of production that leverages technology for improved outcomes.
Benefits of robots in production lines
The benefits of robots in production lines are significant and can transform the efficiency of manufacturing processes. By integrating robots, companies can achieve higher precision and consistency in their products. This leads to fewer errors and a reduction in waste.
Increased Efficiency
Robots work at a fast pace and can handle repetitive tasks without tiring. This allows manufacturers to maintain continuous production. As a result, production lines are more efficient, and output increases significantly.
- Faster Production: Robots can operate 24/7 without breaks or downtime.
- Consistent Quality: Automated processes reduce variability in production.
- Scalability: Robots can be scaled up to meet increasing demand quickly.
Companies that adopt this technology often see a boost in their overall productivity and can respond more swiftly to market changes.
Cost Savings
While the initial investment in robotics may seem high, the long-term savings are undeniable. With robots doing the heavy lifting, companies can minimize labor costs and avoid expenses related to worker injuries.
Additionally, robots decrease the chance of costly errors. This contributes to a more sustainable production model by maximizing resource utilization and minimizing waste. The return on investment can be achieved much sooner than expected due to these factors.
The integration of robots creates a safer work environment. As robots take over hazardous tasks, workers can focus on roles that require critical thinking and creativity. This can lead to higher job satisfaction and better workplace morale.
The benefits of robots are clear: faster production, cost savings, and improved safety. As technology continues to advance, the role of robots in production lines will likely grow even more integral to manufacturing success.
Challenges in integrating robots
Integrating robots into manufacturing processes brings a host of advantages, yet there are challenges in integrating robots that must be considered. Understanding these issues is vital for smooth implementation and long-term success.
High Initial Costs
One significant challenge is the high initial investment required for robotic systems. This includes not only the purchase of the robots themselves but also the costs related to installation, training, and maintenance.
- Capital Expenditure: Companies often spend a large sum upfront, which can be a barrier for smaller businesses.
- Training Employees: Proper training is necessary to ensure employees can work effectively alongside robots.
- Maintenance Expenses: Ongoing maintenance is essential to keep robotic systems running smoothly.
Even with these challenges, many companies find that the long-term benefits often outweigh the initial costs.
Technical Integration Issues
Another challenge companies face is integrating robots with existing systems. This includes compatibility with current production equipment and software. Transitioning to an automated system may not be straightforward.
Getting robots to communicate with other machines can require significant adjustments and programming. It’s important that manufacturers consider:
- Software Compatibility: Ensure the robotic systems can work seamlessly with current software platforms.
- System Upgrades: Some equipment may need to be upgraded or replaced.
- Data Security: Protecting sensitive data during integration is crucial.
Thus, planning and expert consultation become essential to navigate these technical hurdles efficiently.
Lastly, there is the human factor. Resistance to change is common in organizations. Workers may fear losing jobs or struggle to adapt to new technologies. To address this, companies should focus on:
- Effective Communication: Sharing the benefits and importance of robotics with employees.
- Involvement in the Process: Involving staff in the integration process fosters a sense of ownership.
- Ongoing Training: Providing continuous training to help employees develop new skills.
By addressing these challenges in integrating robots, manufacturers can create a more productive and harmonious work environment.
Future trends in robotic manufacturing
The future trends in robotic manufacturing are shaping the evolution of the industry. As technology advances, we can expect to see significant changes in how factories operate. One major trend is the rise of collaborative robots, or cobots, designed to work alongside human workers.
Increased Automation
Automation is becoming more prominent. This allows companies to streamline processes and reduce costs. Robotics will continue to play a central role, allowing even small businesses to adopt advanced manufacturing techniques.
- Smart Factories: The integration of IoT (Internet of Things) with robotics will create intelligent manufacturing systems.
- Data-Driven Decisions: Advanced analytics will help in optimizing production schedules and processes.
- Flexible Manufacturing: Robots can be easily reprogrammed for different tasks, increasing versatility.
This level of automation leads to improved efficiency and productivity, enabling companies to meet evolving customer demands.
Advanced Robotics Technology
Technological advancements are revolutionizing the capabilities of robotic systems. Innovations in AI and machine learning are allowing robots to learn from their environments. This means they can adapt to changes without extensive reprogramming.
Some exciting developments include:
- Enhanced Machine Vision: Robots will be able to perceive and understand their surroundings better.
- Improved Dexterity: Advanced grippers and sensory feedback will enable more delicate tasks.
- Autonomous Mobile Robots: Robots that can navigate and transport materials independently will become more common.
These innovations will not only enhance the efficiency of manufacturing but also open up new applications in various sectors.
Another trend is sustainability. As environmental concerns grow, manufacturers will need to invest in greener technologies. Robots can help optimize resource use and reduce waste, aligning with global sustainability goals.
The future of robotic manufacturing promises remarkable changes. With advancements in automation, technology, and sustainability, industries will continue to evolve, creating fresh opportunities and challenges.
Case studies of successful robot implementations
Examining case studies of successful robot implementations reveals the transformative impact of robotics in various industries. These real-world examples demonstrate how companies leverage robots to enhance efficiency, improve quality, and reduce costs.
Automotive Industry
One of the leading sectors using robotics is the automotive industry. For instance, a major car manufacturer adopted robots for assembly line tasks. By integrating robotic arms for painting and welding, they achieved significant improvements.
- Efficiency: The robots reduced production time by up to 30%.
- Quality: Consistent precision led to fewer defects in finished vehicles.
- Cost Reduction: The company saved on labor costs and reduced waste.
This case clearly shows how robotics can revolutionize traditional manufacturing processes.
Electronics Manufacturing
Another compelling example comes from the electronics sector. A leading electronics manufacturer implemented robots in their production of smartphones. The robots handled delicate components with care, which improved overall quality.
Some highlights from this case include:
- Increased Speed: The robotic integration sped up production rates significantly.
- Quality Control: Enhanced vision systems helped detect defects at an early stage.
- Workforce Efficiency: Human workers could focus on complex assembly tasks.
As a result, customer satisfaction improved due to higher quality products.
In food processing, robots have also made a mark. A well-known food company used robots for sorting and packaging. This implementation led to:
- Increased Output: The robots handled high volumes of products quickly.
- Better Hygiene: Automated processes reduced contamination risks.
- Reduced Labor Costs: Fewer workers were needed for repetitive tasks.
This case illustrates the versatility of robots in various applications.
These successful robot implementations emphasize the growing role of automation in enhancing productivity and quality across different sectors. By studying these cases, other companies can derive valuable insights into the benefits of robotics.
FAQ – Frequently Asked Questions about Robots in Manufacturing
What are the main benefits of using robots in manufacturing?
Robots improve efficiency, reduce costs, and enhance product quality by performing tasks with precision and consistency.
How can small companies afford robotic automation?
Many robotic solutions are now available at various price points, and the long-term savings often outweigh initial investment costs.
What challenges do companies face when integrating robots?
Challenges include high initial costs, technical integration issues, and potential resistance from employees.
How can robotics improve worker safety?
By taking over hazardous tasks, robots help reduce workplace injuries, allowing employees to focus on safer, more complex duties.